D2 Steel Knife 101
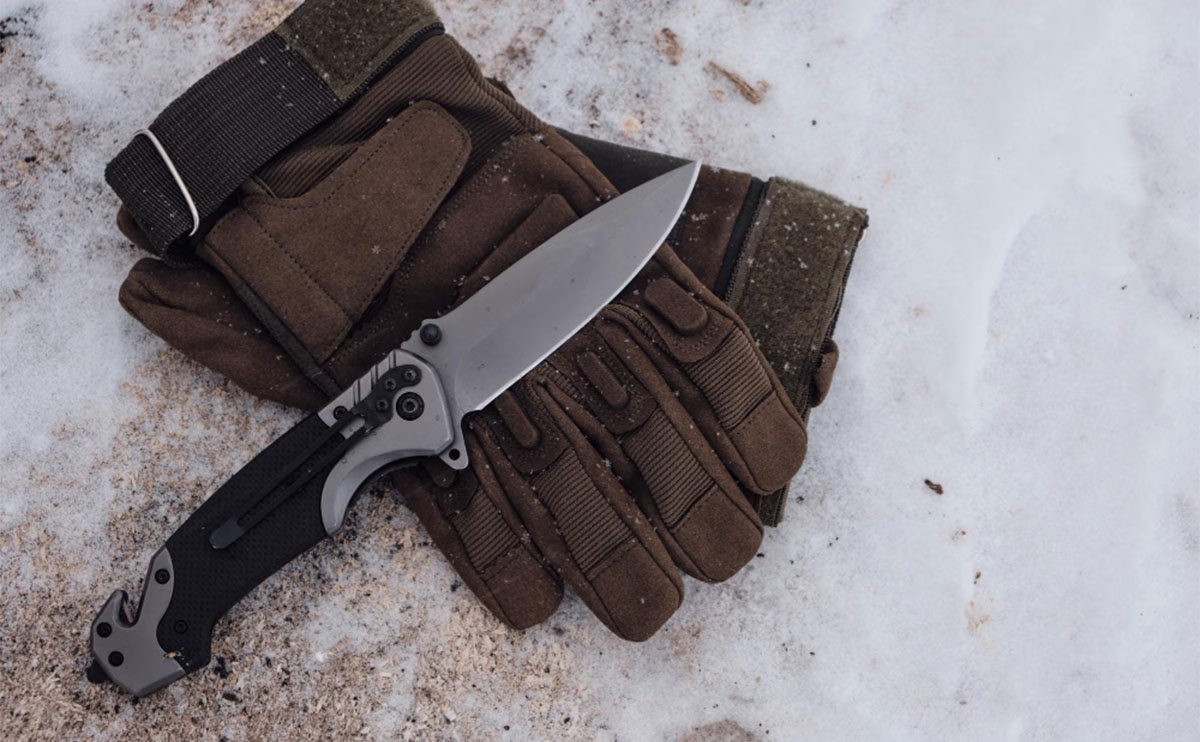
Table of Contents
Introduction to D2 Steel in Knife Making:
D2 steel, a designation within the family of tool steels, represents a material widely utilized in the creation of high-performance knives. Classified as a high-carbon, high-chromium steel, it falls under the category of cold-work tool steels, specifically within the D-series. This classification signifies its suitability for applications demanding significant wear resistance and durability, even at lower temperatures. Globally recognized, D2 steel is known by various alternative designations, including SKD11 in Japan, 1.2379 in Germany, Hitachi SLD, and Uddeholm Sverker 21. Its origins trace back to the early 20th century, emerging as a response to the growing need for robust tool steels capable of withstanding the rigors of industrial operations. Initially, D2 steel found primary application in the manufacturing of industrial cutting implements such as dies, drills, and saw blades. This initial utilization underscores the steel’s inherent capacity to resist wear and maintain a sharp cutting edge under demanding conditions, properties that would later prove highly advantageous in the realm of knife making.
The transition of D2 steel into the knife-making industry marked a significant development, driven by its exceptional balance between the crucial properties of edge retention and toughness. For many knife makers and enthusiasts, D2 steel is considered a top-tier option, even earning the description of being among the best carbon steels for crafting blades. While technically classified as semi-stainless steel due to its chromium content, its performance characteristics often place it in a similar category to high-carbon steels regarding edge retention. Furthermore, D2 steel often occupies a favorable position in the market, offering a compelling combination of performance and affordability, frequently found in the lower to medium-price segments of the knife market. The initial selection of D2 steel for demanding industrial cutting applications laid the groundwork for its successful adoption in knife making. The properties that make it suitable for industrial tools, namely wear resistance and edge durability, are precisely those sought after in high-quality knife blades.
Understanding D2 Steel: Composition and Properties:
D2 steel is a high-carbon, high-chromium tool steel widely used in knife making due to its excellent wear resistance and ability to maintain a sharp edge. It typically contains 1.40% to 1.60% carbon (around 1.5%), which contributes to its hardness, and 11.00% to 13.00% chromium (around 12%), offering moderate corrosion resistance. Though not fully stainless, its chromium content provides better protection than other high-carbon steels. The steel also contains 0.70% to 1.20% molybdenum (around 0.8%) for improved toughness and machinability, and 0.60% to 1.00% vanadium (around 0.9%) for added wear resistance and hardness.
Minor elements like silicon (max 0.3%) and manganese (max 0.5%) help with strength, while trace amounts of phosphorus, sulfur, nickel, copper, and cobalt may also be present. The exact composition can vary depending on the manufacturer, with D2 produced by Markforged meeting ASTM A681 standards.
D2 steel typically achieves a hardness of 55-62 HRC, making it ideal for tools requiring edge retention. However, it is less tough than some steels like 1095 and can be prone to chipping if mishandled or improperly heat-treated. Tempering at lower temperatures helps improve toughness and reduce brittleness.
While D2 steel is not fully stainless, its 12% chromium provides moderate corrosion resistance, making it suitable for environments where rust prevention is necessary. However, proper care is still needed, especially in humid or acidic conditions. D2’s high wear resistance and dimensional stability, combined with its density of 7.7 g/cm³, make it a popular choice for durable knife blades, though its poor machinability (27% compared to AISI 1112) can make it challenging to work with.
In summary, D2 steel offers a strong balance of wear resistance, edge retention, and corrosion resistance, making it an excellent choice for high-performance knives.
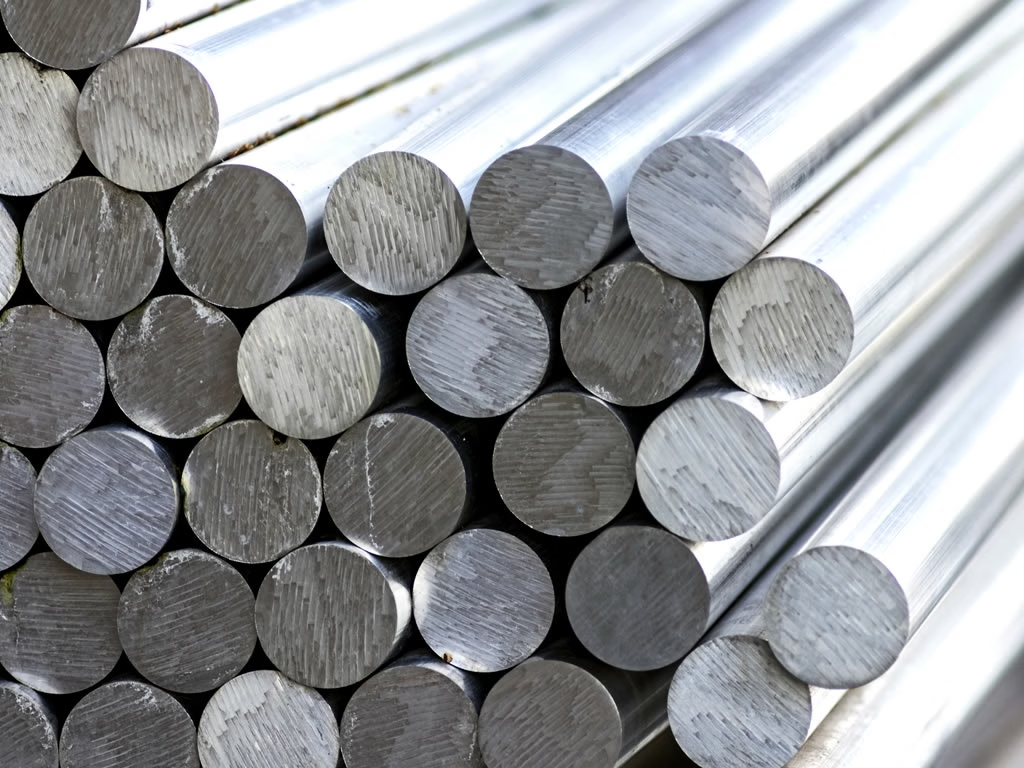
Applications in the Blade Industry: Common D2 steel knife:
D2 steel’s versatile property set has led to its widespread use in the manufacturing of a diverse range of knife types. Its balance of edge retention, toughness, and moderate corrosion resistance makes it suitable for various applications. One of the most common applications is in pocket knives, particularly those intended for everyday carry (EDC). The steel’s ability to maintain a sharp edge through daily tasks, coupled with its reasonable resistance to rust, makes it a practical choice for EDC blades. Outdoor enthusiasts also frequently turn to knives made from D2 steel, where durability and edge retention are crucial for tasks encountered in the field. Similarly, work knives often utilize D2 steel due to its wear resistance, allowing them to withstand the rigors of demanding work environments. For bushcraft knives, D2 steel’s strength and capacity to hold a fine edge make it a popular material, capable of handling tasks in harsh environmental conditions. Tactical knives, designed for demanding use, also benefit from D2 steel’s toughness and wear resistance. Hunters appreciate the edge retention of D2 steel in their hunting knives, as a sharp blade is essential for processing the game. Even in the culinary world, chef’s knives made from D2 steel are gaining popularity due to their toughness, durability, and excellent edge retention. However, their lower corrosion resistance compared to some stainless steels requires more careful maintenance. D2 steel is used in both fixed and folding blades, demonstrating its adaptability across different knife designs and mechanisms. Its initial industrial applications in slitter and shear blades further highlight its inherent wear resistance, while its use in food-processing knives indicates its suitability for culinary purposes with proper care. The prevalence of D2 steel in knives designed for challenging applications like bushcraft and tactical use underscores its reputation for reliable performance under stress. Numerous manufacturers and brands have embraced D2 steel for their knife offerings. The sheer number of brands and knife types incorporating D2 steel across various retailers and manufacturers strongly suggests a robust market presence and significant consumer demand for knives made from this material. This widespread adoption indicates a generally positive perception of D2 steel’s performance and overall value within the knife community.
The Competitive Edge: Advantages of Using D2 Steel Knives:
One of the most significant advantages of using D2 steel in knife making is its superior edge retention. This is primarily attributed to its high carbon content and exceptional resistance to wear. Users of D2 steel knives often report that the blade maintains its sharpness for extended periods, requiring less frequent sharpening compared to knives made from many other steel types. One source even considers D2 steel to be the “best bang for your buck steel for edge retention,” highlighting its strong performance relative to its cost. This exceptional edge retention is a key factor driving the popularity of D2 steel among knife enthusiasts and professionals alike.
The high hardness of D2 steel, typically ranging from 55 to 62 HRC, directly contributes to its excellent wear resistance. This hardness allows the blade to withstand significant impact and wear, making D2 steel knives a durable choice for heavy use. It is particularly well-suited for cutting and slicing tasks where the blade’s edge is subjected to prolonged wear over time. The inherent hardness of the steel resists deformation and abrasion, ensuring that the cutting edge remains effective even after extensive use of various materials.
While D2 steel is sometimes perceived as being brittle, especially when compared to very tough steels like 1095, it is generally considered to possess good toughness, particularly when it has undergone proper heat treatment. When correctly processed, D2 steel can be quite durable and resistant to chipping, cracking, and breaking under normal usage conditions. It strikes a favorable balance between the crucial properties of wear resistance and toughness, making it a versatile material for a wide array of knife applications. The emphasis on proper heat treatment is critical, as it is the key to maximizing the steel’s toughness and minimizing the risk of brittleness.
Compared to many other high-carbon, non-stainless steels, D2 steel offers a significant advantage in terms of corrosion resistance due to its chromium content. While it does not meet the criteria to be classified as fully stainless, it still provides a notable degree of protection against rust and staining and is often referred to as “semi-stainless”. This level of corrosion resistance makes D2 steel a more practical option for everyday use compared to traditional carbon steels, which are highly susceptible to rust and require more meticulous maintenance.
Finally, D2 steel often presents a cost-effective option when compared to some premium knife steels like S30V, while still offering a similar level of high-quality performance in terms of edge retention. It can typically be found in the lower to medium price segments of the knife market, providing a strong ratio of performance to cost. Furthermore, the inherent durability and excellent edge retention of D2 steel knives can potentially lead to lower long-term costs for users, as they require less frequent sharpening and may need replacement less often. This combination of performance and affordability makes D2 steel an attractive choice for a wide range of knife users.
Addressing the Limitations: Disadvantages of Using D2 Steel Knives:
Despite its numerous advantages, D2 steel also presents certain limitations that users should consider. One of the most frequently cited drawbacks is the difficulty encountered when sharpening knives made from this steel. This difficulty arises from the steel’s high hardness and exceptional wear resistance, the very properties that contribute to its excellent edge retention. Sharpening D2 steel often requires the use of specific tools and techniques, which may include diamond sharpening stones, as traditional methods might prove less effective. The process can also be more time-consuming compared to sharpening knives made from softer steel alloys.
Another limitation of D2 steel is that it is not fully stainless. While it offers moderate corrosion resistance, it is still susceptible to rust, particularly if not properly cared for, especially when exposed to moisture, acidic substances, or saltwater. This necessitates regular cleaning and thorough drying after each use, and the application of a protective layer of oil might be required to prevent corrosion, especially in humid environments. This requirement for more diligent maintenance is a key difference compared to fully stainless steel knives.
There is also a potential for brittleness and chipping with D2 steel, especially if the blade has not been properly heat-treated during manufacturing or if the knife is subjected to misuse. Compared to tougher steels like 1095, D2 steel can be more prone to chipping under certain conditions. Therefore, it is generally not recommended for tasks that involve excessive lateral force or prying, as these actions can potentially damage the blade. Users need to be mindful of the intended use of a D2 steel knife and avoid subjecting it to undue stress.
From a manufacturing perspective, D2 steel is known for its poor machinability.1 Its high hardness and carbon content make it difficult to shape and finish during the knife-making process. This can potentially lead to higher manufacturing costs, although this is not always directly reflected in the final price for the consumer. The difficulty in machining D2 steel might also limit the complexity of designs or finishes that can be easily achieved compared to more machinable steels.
Finally, while D2 steel is renowned for its edge retention, some users have reported that it can be challenging to achieve an exceptionally fine, razor-like edge. One perspective suggests that D2 steel might take a “crappy edge and hold it forever,” implying that while it stays sharp for a long time, the initial sharpness might not be as acute as with some other steels. However, this view is not universally held, with other sources stating that D2 steel has very high sharpness potential and is relatively easy to hone. This discrepancy likely reflects varying user experiences and sharpening skills.
D2 Steel Versus the Competition: A Comparative Analysis with Other Knife Steels:
When evaluating D2 steel as a knife-making material, it is beneficial to compare it with other commonly used steels, such as stainless steels like 440C, AUS-8, and S30V, as well as traditional carbon steels like 1095. In terms of corrosion resistance, stainless steels generally outperform D2 steel due to their higher chromium content. For instance, 440C offers better rust resistance than D2. However, D2 steel typically exhibits superior edge retention compared to many common stainless steels like 440C and AUS-8. While premium stainless steels such as S30V might offer comparable or even better edge retention than D2, they often come at a higher cost. Notably, one test indicated that S30V held an edge approximately 13% longer than D2. The toughness of D2 steel is generally considered good, but some stainless steels might offer better toughness, while others might be similar or less tough, depending on the specific alloy and heat treatment. For example, 8Cr13MoV, with a lower carbon content, might provide higher strength and edge toughness at similar hardness levels compared to D2. Sharpening is another area where D2 differs from many stainless steels; alloys like AUS-8 and 8Cr13MoV are generally easier to sharpen than D2. In terms of cost, D2 steel often occupies a middle ground, typically being more expensive than budget stainless steels but less so than high-end options like S30V.
Compared to traditional carbon steels like 1095, D2 steel offers significantly better corrosion resistance. While carbon steels are known for their ability to take a very fine edge and are generally easier to sharpen, D2 steel typically provides superior edge retention. However, some carbon steels, such as 1095, are renowned for their high toughness, which might exceed that of D2 steel.
The following table provides a comparative overview of D2 steel with some other common knife steels across key properties:
Steel | Hardness (HRC) | Toughness | Corrosion Resistance | Edge Retention | Sharpening Ease | Cost |
D2 | 55-62 | Good | Moderate | Excellent | Difficult | Mid-Range |
440C | 57-60 | Moderate | Good | Good | Moderate | Low-Mid |
AUS-8 | 57-59 | Moderate | Moderate-Good | Moderate | Easy | Low |
S30V | 58-61 | Good | Good | Very High | Difficult | High |
1095 | 56-58 | Very High | Poor | Moderate | Easy | Low |
This comparison illustrates the trade-offs inherent in different steel alloys. D2 steel stands out for its excellent edge retention and good toughness, coupled with moderate corrosion resistance, positioning it as a strong contender for users who prioritize these characteristics.
The Cost Factor: Typical Price Range for D2 Steel Knives:
D2 steel knives are available across a broad spectrum of price points, catering to various budgets and preferences. One source suggests a typical price range of approximately $50 to $120 for D2 steel knives. However, more affordable options can be found, with some models listed on online marketplaces like Amazon and Walmart for under $30 and even below $20. Conversely, higher-end D2 steel knives, often featuring premium handle materials, intricate designs, or from renowned manufacturers, can exceed this typical range. For example, Honeybadger Knives offers their D2 steel blade knives in the $56 to $79 price bracket , while Tosahwi Knife features D2 steel models ranging from around $28 to $80. KnifeCenter’s selection of “Best Affordable D2 Steel Knives” includes options priced from approximately $12 to $60. This wide variation in price indicates that while D2 steel itself offers a good balance of performance and cost, the final price of a D2 steel knife is also influenced by factors such as brand reputation, design complexity, the quality of handle materials, and the overall craftsmanship.
The reputation of the brand plays a significant role in pricing, with well-established and respected manufacturers often commanding higher prices. The complexity of the knife’s design, including the blade shape, handle ergonomics, and locking mechanisms (for folding knives), also contributes to the cost. The materials used for the handle, such as premium options like titanium or high-end micarta, will invariably increase the price compared to more basic materials like FRN or standard G10. Furthermore, the overall build quality and the precision of the knife’s construction are factors that can justify a higher price point. Even the specific heat treatment process employed by the manufacturer can influence the cost, as more controlled and precise methods might involve higher production expenses. Therefore, when considering the price of a D2 steel knife, it is important to look beyond just the type of steel and evaluate the overall package, including the brand, design, materials, and the reputation of the manufacturer for quality and performance.
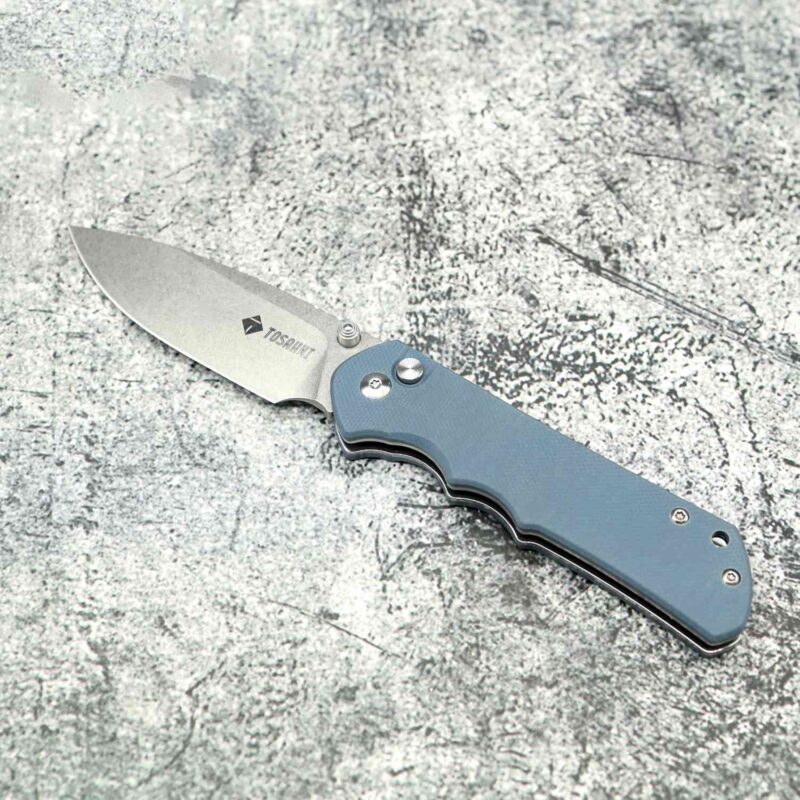
Preserving the Edge: Care and Maintenance Requirements for D2 Steel Knives:
Maintaining a D2 steel knife properly is crucial for preserving its performance and preventing corrosion, given its semi-stainless nature. Regular cleaning and drying after each use are paramount. The blade should be washed with mild soap and warm water to remove any food particles, dirt, or other residues that could potentially lead to corrosion. It is essential to dry the blade thoroughly immediately after washing with a clean cloth to prevent any moisture from lingering on the surface, which could initiate rust formation. Dishwashers should be avoided as the high heat and harsh detergents can be detrimental to both the blade and the handle materials.
Applying a thin layer of mineral oil or food-grade oil to the blade periodically can provide an extra layer of protection against rust, especially if the knife is not used frequently or if it is stored in a humid environment. For folding knives, lubricating the pivot points with a few drops of appropriate oil will help ensure smooth operation of the mechanism. Proper storage is also important for maintaining the condition of a D2 steel knife. It should be stored in a dry, cool place, ideally in a sheath, knife block, or on a magnetic strip, which will protect the blade from physical damage and minimize exposure to moisture. Storing knives loosely in drawers with other utensils should be avoided as it can lead to scratches and potential dulling of the blade’s edge.
Sharpening a D2 steel knife requires appropriate tools and techniques due to its high hardness. Sharpening stones, honing oil, and angle guides are recommended for achieving and maintaining a sharp edge. For very dull edges or for reprofiling the blade, diamond sharpening stones might be necessary as they are more effective on hard steels. Regular honing with a honing rod between sharpenings can help to realign the blade’s edge and prolong the need for full sharpening. If the user is uncomfortable with sharpening D2 steel, seeking professional sharpening services is a viable option.
It is also important to avoid using harsh chemicals or abrasive cleaners on D2 steel blades, as these can damage the finish and potentially the steel itself. The knife should be used for its intended purpose – cutting and slicing – and actions like twisting or prying should be avoided as they can lead to chipping or breakage, especially given D2’s potential for brittleness if subjected to excessive stress. Cutting acidic substances or saltwater should be followed by immediate and thorough cleaning to prevent accelerated corrosion. Finally, users should be aware that some discoloration on a D2 steel blade might be patina, a natural oxidation process that can offer a degree of protection, rather than harmful red rust. However, even with patina formation, regular cleaning and oiling are still recommended to prevent true rust from developing and compromising the integrity of the blade.
Conclusion: A Comprehensive Assessment of D2 Steel for Knife Making:
In conclusion, D2 steel stands out as a compelling material for knife making, characterized by its high hardness, exceptional edge retention, good toughness when properly heat-treated, and moderate corrosion resistance. These properties make it a popular choice for a wide range of knife types, from everyday carry folders to robust outdoor and tactical blades. While its superior edge retention is a significant advantage, users should be aware of the trade-off, which includes a greater difficulty in sharpening compared to softer steels and the need for diligent maintenance to prevent rust due to its semi-stainless nature. The potential for brittleness if improperly treated or misused also requires consideration.
D2 steel is particularly well-suited for individuals who prioritize a blade that can maintain a sharp edge for extended periods and are willing to invest the time and effort in proper care and potentially more challenging sharpening techniques. Its cost-effectiveness compared to some premium steels further enhances its appeal to a broad range of knife enthusiasts. Despite the emergence of newer steel alloys in the market, D2 steel has maintained its strong reputation and continues to be a widely used and respected material in the knife-making industry, offering a reliable balance of performance and value.